گرافیت یک ماده غیرفلزی رایج، سیاه رنگ، با مقاومت دمایی بالا و پایین، رسانایی الکتریکی و حرارتی خوب، روانکاری خوب و ویژگیهای شیمیایی پایدار است. رسانایی الکتریکی خوب، میتواند به عنوان الکترود در EDM استفاده شود. در مقایسه با الکترودهای مسی سنتی، گرافیت مزایای بسیاری مانند مقاومت در برابر دمای بالا، مصرف تخلیه کم و تغییر شکل حرارتی کوچک دارد. این ماده سازگاری بهتری در پردازش قطعات دقیق و پیچیده و الکترودهای بزرگ نشان میدهد. به تدریج به عنوان جرقه الکتریکی جایگزین الکترودهای مسی شده است. جریان اصلی الکترودهای ماشینکاری [1]. علاوه بر این، مواد مقاوم در برابر سایش گرافیت را میتوان در شرایط سرعت بالا، دمای بالا و فشار بالا بدون روغن روانکاری استفاده کرد. بسیاری از تجهیزات به طور گسترده از کاسه پیستون، آببند و یاتاقانهای گرافیتی استفاده میکنند.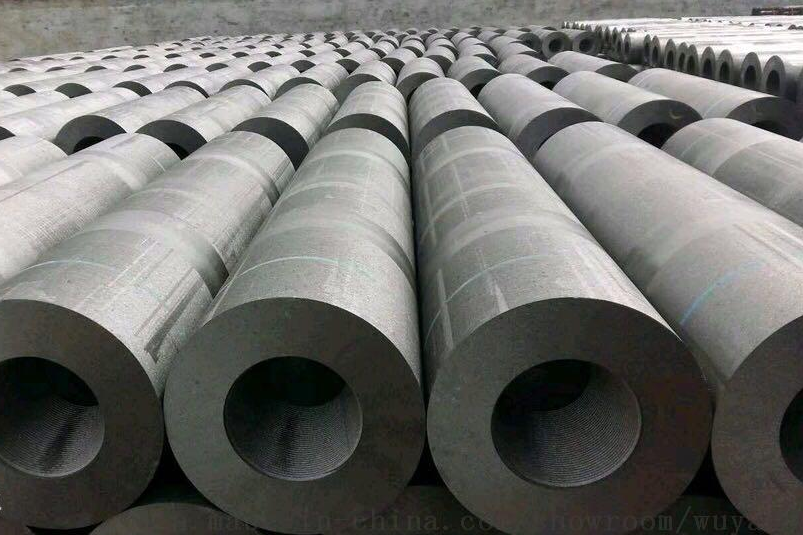
در حال حاضر، مواد گرافیتی به طور گسترده در زمینههای ماشینآلات، متالورژی، صنایع شیمیایی، دفاع ملی و سایر زمینهها مورد استفاده قرار میگیرند. انواع مختلفی از قطعات گرافیتی، ساختار قطعات پیچیده، دقت ابعادی بالا و الزامات کیفیت سطح وجود دارد. تحقیقات داخلی در مورد ماشینکاری گرافیت به اندازه کافی عمیق نیست. ماشینآلات پردازش گرافیت داخلی نیز نسبتاً کم هستند. پردازش گرافیت خارجی عمدتاً از مراکز پردازش گرافیت برای پردازش پرسرعت استفاده میکند که اکنون به جهت اصلی توسعه ماشینکاری گرافیت تبدیل شده است.
این مقاله عمدتاً فناوری ماشینکاری گرافیتی و ماشینهای ابزار پردازش را از جنبههای زیر تجزیه و تحلیل میکند.
① تجزیه و تحلیل عملکرد ماشینکاری گرافیت؛
② اقدامات معمول فناوری پردازش گرافیت؛
③ ابزارهای متداول و پارامترهای برش در پردازش گرافیت؛
تجزیه و تحلیل عملکرد برش گرافیت
گرافیت مادهای شکننده با ساختار ناهمگن است. برش گرافیت با تولید ذرات یا پودر تراشه ناپیوسته از طریق شکست شکننده ماده گرافیتی حاصل میشود. در مورد مکانیسم برش مواد گرافیتی، محققان در داخل و خارج از کشور تحقیقات زیادی انجام دادهاند. محققان خارجی معتقدند که فرآیند تشکیل تراشه گرافیت تقریباً زمانی است که لبه برش ابزار با قطعه کار تماس پیدا میکند و نوک ابزار خرد میشود و تراشههای کوچک و گودالهای کوچکی تشکیل میدهد و ترکی ایجاد میشود که به جلو و پایین نوک ابزار گسترش مییابد و گودال شکستگی تشکیل میدهد و بخشی از قطعه کار به دلیل پیشروی ابزار شکسته میشود و تراشهها را تشکیل میدهد. محققان داخلی معتقدند که ذرات گرافیت بسیار ریز هستند و لبه برش ابزار دارای قوس نوک بزرگی است، بنابراین نقش لبه برش مشابه اکستروژن است. ماده گرافیتی در ناحیه تماس ابزار - قطعه کار توسط سطح چنگک و نوک ابزار فشرده میشود. تحت فشار، شکستگی شکننده ایجاد میشود و در نتیجه تراشههای خرد شده تشکیل میشوند [3].
در فرآیند برش گرافیت، به دلیل تغییر در جهت برش گوشههای گرد یا گوشههای قطعه کار، تغییر در شتاب ابزار ماشین، تغییر در جهت و زاویه برش داخل و خارج ابزار، لرزش برش و غیره، ضربه خاصی به قطعه کار گرافیتی وارد میشود و در نتیجه لبه قطعه گرافیتی دچار شکنندگی و لب پریدگی گوشه، سایش شدید ابزار و سایر مشکلات میشود. به خصوص هنگام پردازش گوشهها و قطعات گرافیتی نازک و باریک، احتمال ایجاد گوشهها و لب پریدگی قطعه کار بیشتر است که این امر در ماشینکاری گرافیت نیز به یک مشکل تبدیل شده است.
فرآیند برش گرافیت
روشهای سنتی ماشینکاری مواد گرافیتی شامل تراشکاری، فرزکاری، سنگزنی، ارهکاری و غیره است، اما آنها فقط میتوانند پردازش قطعات گرافیتی با اشکال ساده و دقت پایین را انجام دهند. با توسعه سریع و کاربرد مراکز ماشینکاری پرسرعت گرافیتی، ابزارهای برش و فناوریهای پشتیبانی مرتبط، این روشهای سنتی ماشینکاری به تدریج با فناوریهای ماشینکاری پرسرعت جایگزین شدهاند. تجربه نشان داده است که: به دلیل ویژگیهای سخت و شکننده گرافیت، سایش ابزار در حین پردازش جدیتر است، بنابراین توصیه میشود از ابزارهای روکشدار کاربیدی یا الماسی استفاده شود.
اقدامات فرآیند برش
با توجه به ویژگی خاص گرافیت، برای دستیابی به پردازش با کیفیت بالا در قطعات گرافیتی، باید اقدامات فرآیندی مربوطه انجام شود تا اطمینان حاصل شود. هنگام خشنکاری مواد گرافیتی، ابزار میتواند مستقیماً با استفاده از پارامترهای برش نسبتاً بزرگ، روی قطعه کار تغذیه شود. برای جلوگیری از لبپریدگی در حین پرداخت، اغلب از ابزارهایی با مقاومت سایشی خوب برای کاهش میزان برش ابزار استفاده میشود و اطمینان حاصل میشود که گام ابزار برش کمتر از 1/2 قطر ابزار است و هنگام پردازش هر دو انتها، اقدامات فرآیندی مانند پردازش کاهش سرعت انجام میشود [4].
همچنین لازم است مسیر برش در حین برش به طور منطقی تنظیم شود. هنگام پردازش کانتور داخلی، کانتور اطراف باید تا حد امکان برای برش قسمت نیروی قطعه برش داده شده استفاده شود تا همیشه ضخیم تر و قوی تر باشد و از شکستن قطعه کار جلوگیری شود [5]. هنگام پردازش صفحات یا شیارها، تا حد امکان تغذیه مورب یا مارپیچی را انتخاب کنید. از ایجاد جزایر روی سطح کار قطعه خودداری کنید و از بریدن قطعه کار روی سطح کار خودداری کنید.
علاوه بر این، روش برش نیز عامل مهمی است که بر برش گرافیت تأثیر میگذارد. ارتعاش برش در طول فرزکاری رو به پایین کمتر از فرزکاری رو به بالا است. ضخامت برش ابزار در طول فرزکاری رو به پایین از حداکثر به صفر کاهش مییابد و پس از برش ابزار در قطعه کار، پدیده پرش وجود نخواهد داشت. بنابراین، فرزکاری رو به پایین معمولاً برای پردازش گرافیت انتخاب میشود.
هنگام پردازش قطعات گرافیتی با ساختارهای پیچیده، علاوه بر بهینهسازی فناوری پردازش بر اساس ملاحظات فوق، باید اقدامات خاصی نیز با توجه به شرایط خاص انجام شود تا بهترین نتایج برش حاصل شود.
زمان ارسال: ۲۰ فوریه ۲۰۲۱